Air Filter Gages and Switches
Air Filter Gages and Switches
The application of . . .
Air filters used in ventilating systems are called upon to remove an extremely wide variety of contaminants from the air, ranging from soot and smoke and the common dusts to mold spores, bacteria and pollen. Particle sizes vary from less than a micron (.000039") to insects and leaves. The concentration will vary hourly, daily and seasonally.
These variables combined with filtering requirements that range from the simple needs of a household furnace to the absolute filtration required for a clean room make air cleaning a complex science. Filter selection should, therefore, be made by a qualified engineer or in cooperation with the filter manufacturer.
The same variables that affect filter selection also contribute to the problem of determining when a filter has reached the tolerable limit of its effective life span as a result of the accumulation of contaminants. Because of wide variation in contaminant load in the air being filtered, time is an uncertain measurement. Visual inspection of the condition of the filter tells little or nothing. The most widely used method of checking filter condition is to measure pressure drop across the filter by means of an air filter gage.
The Function of the Air Filter Gage
A clarification of terminology is essential to understanding the function of an air filter gage. The air filter gage measures pressure drop across the filter for the purpose of determining whether or not the filter is operating within its design range of effective utilization. It does not measure filter efficiency.
Filter efficiency as defined by the ASHRAE GUIDE, "is synonymous with the term arrestance and measures the ability of the air cleaner to remove particulate matter from an air stream." Several methods of determining filter efficiency exist, because of variations in filters and application requirements.
One method is by weight, in which a carefully compounded mixture of standardized dust is fed into the air stream and the amount trapped by the filter related to the amount released in the test determines the filter efficiency in percentage. A second method, the dust spot method originated by the National Bureau of Standards, compares the opacity of the dust collected on filter paper from two air samples of equal flow rate, one of which samples filtered air. The efficiency of filter is thus evaluated on the basis of the darkness of the dust spots. A third method measures arrestance of DOP (Dioctyl-phthalate) smoke, a homogenous aerosol of 0.3 micros size, to test a special class of high efficiency filters used to control particulate matter of high toxicity or where extreme cleanliness is required.
The "dust holding capacity" of an air filter is defined by ASHRAE GUIDE as, "the amount of a particular dust that an air filter can hold and determines the operating life the air cleaner which is fixed mainly by some figure of tolerable resistance." Thus, an air filter gage, sensing the differential in static pressure across an air filter, will permit the air filter to be used to its maximum dust holding capacity as determined by the filter manufacturer and specified in terms of maximum filter resistance. It should be noted that servicing a filter when it has reached its point of specified maximum resistance is the only method which will guarantee that the filters are being used beyond the point where their increased resistance could affect balance of the system, increase air leakage and, for some types of filters, begin to pass contaminants.
Type of Filters and Recommended Resistance for Servicing
All filter manufacturers supply technical data which will permit full utilization of their filters. This data will include initial resistance in inches of water column for the filter at its rated air flow and a recommended resistance at which point the filter should be replaced or serviced. The following describes the broad classifications of air filters:
Viscous Impingement Filters have the filter element treated with an oil or adhesive which holds dust particles coming in contact. The initial resistance of a typical filter will usually run from .08 to .15" water, and servicing will be called for at .50" water by means of a pressure actuated switch or timer with overriding pressure switch operating an electrical drive.
Dry Type Filters are available in a multiplicity of materials, in varying thicknesses, in batts, woven or bonded materials, natural or synthetic, and in pleated form or in tubes or bags to obtain greater filter area. Efficiencies are usually at least equivalent to the viscous impingement type and may run to virtually 100%. Dust holding capacity is high and resistance values vary so widely no rule of thumb figures are possible. The manufacturer should always be consulted for proper initial and final pressure drop figures for these filters.
Electronic Air Cleaners using the electrostatic precipitation principle have no characteristic increase in pressure drop as they accumulate dust and must therefore be serviced on a pre-set schedule. The mechanical filter normally used with such equipment should, however, be serviced on the basis of increased pressure drop.
Significance of High or Low Initial Resistance Readings due to the many variables inherent in an air distribution system, the initial pressure drop in some systems may be found to be below that specified by the filter manufacturer. If the system has been carefully checked over and found to be in order, this need not be a source of concern, as it simply indicates that less than rated air volume is passing through the filter. Generally, this will mean increased filter life before the filter requires servicing. Conversely, if initial pressure drop exceeds the filter manufacturer's rating, it indicates that a greater volume of air is being handled than the filter is rated for and filter life will be shortened.
Excessive variation from the filter manufacturer's published initial resistance figure will probably indicate one or more of the following problems:
Low Pressure Drop
- Less than rated air volume being handled due to over design of filter area, improper air balancing of system, open bypasses, etc.
- Incorrect filter installed.
- Velocity influence.
- Air leakage around filters, past frames, and possibly through damaged filter.
IMPORTANT: An initial pressure drop 30% to 40% or more below the rated value for the filter means that approach velocities may be sufficiently low to impair the efficiency of some types of filters.
- Incorrect filter installed.
- System handling more than rated air volume. Suggest thorough check of system to be certain all controls are properly set and operating. If unable to reduce pressure drop to less than ten percent or fifteen percent above rated value additional filter area should be provided or air volume reduced.
IMPORTANT: An initial pressure drop 10% to 15% or more above the rated value for the filter, means that approach velocities may be sufficiently high to impair the efficiency of some types of filters.
Before putting your air filter gage into service or in the event of initial pressure drop readings that don't agree with the filter manufacturer's specified pressure drop, make the following checks:
- Check zero adjustment of the gage. Remove both tubing leads or open vent valves to atmosphere.
- Check all tubing connections for tightness from gage to the static tip or fitting connection.
- Check static pressure tips or fittings to be sure they are not plugged.
- Check installation of static tips or fittings. Angle type static pressure tips must point directly into the air stream. Flange type static pressure fittings should be mounted on a duct wall in such a location that the opening is at a right angle to the moving air stream. A velocity pressure error can be created if the air blows directly into the opening.
How to Install Dwyer Air Filter Gages and Switches
Dwyer Air Filter Gages and Switches are offered in a variety of types to meet the needs of your system. All types are customarily mounted on the outside of the air handling duct or plenum near the filter bank.
The type of static pressure tips used and their location is of primary importance in securing reliable readings. For maximum accuracy, it is essential that the influence of the velocity of the air be eliminated to permit sensing the true static pressure. Note that some filter installations do not provide a straight duct approach to the filter bank which may cause air to swirl and eddy.
Right angle static pressure tips give the most accurate sensing and are furnished with Series 2000 Magnehelic® Gages and Series 250-AF Gages. Flush static pressure fittings inserted at right angles to the flow are lower in cost and less likely to plug up, but are more susceptible to velocity and turbulence influence.
Tips should be located as recommended by the specifying engineer or by the filter manufacturer. In the absence of such recommendations, locate the tips at least 12" upstream and downstream from the filters in a zone of minimum turbulence.
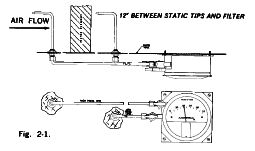
Fig. 2-1. Series 2000 Magnehelic® Gages are diaphragm actuated pointer type gages. The gage is attached to the mounting plate which is furnished and the mounting plate screwed to the wall of the air duct. The static pressure tips are installed through 7/16" holes in the filter wall with tips pointed into air flow. The static tips are connected to the plastic vent valves using the 1/4" aluminum tubing and compression fittings which are furnished. Zeroing is accomplished by turning the vent valves to venting position and then turning the zero adjustment screw in the face of the gage with a screwdriver. For detailed instructions, see Bulletins A-27 and A-28.
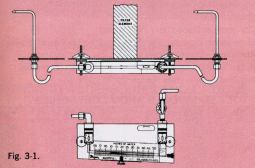
Fig. 3-1. Series 250-AF Solid Plastic Gages are manometer type gages which are customarily mounted directly on the wall of the filter housing. The static pressure tips are installed through 7/16" holes in the filter wall with tips pointing into the air flow using the 1/4" aluminum tubing and compression fittings which are furnished. Zeroing is accomplished by turning the vent valves (optional at extra cost) to "vent" position - or by pulling the connections from the gage body if vent valves are not used - and sliding the adjustable scale until the zero mark lies directly behind the indicating fluid meniscus.
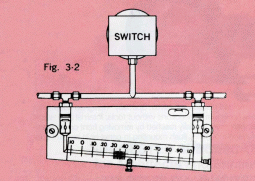
Fig. 3-2. Shows a typical hook-up of a Model 1823 compact, diaphragm actuated differential pressure switch in parallel with a gage using tees. The switch is set to energize an electric circuit when the maximum allowable pressure drop is reached.
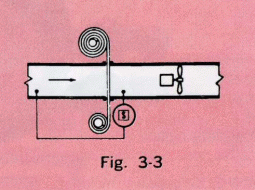
Fig 3-3. Shows schematically how a Model 1638 switch with visual set point adjustment can be hooked up to trigger the advancement of an automatic roll filter when the segment in use becomes too dirty for efficient service.
For detailed instructions, see Bulletins E-552 (Model No. 1638), E-53 (Model No. 1823) and E-55 (Air filter switch service).