Flowmeters and Sight Flow Indicators
Flowmeters and Sight Flow Indicators
How Flowmeters Work
Variable area flowmeters are basically vertical internally tapered tubes mounted with the large end at the top. A float or rotor with an outer diameter slightly less than the minimum diameter of the tube is placed inside the tube. The clearance space between the float and the tube forms an annular passage or orifice. As the tube is tapered, the area of this orifice is larger when the float is near the top than it is when the float is near the bottom. By connecting the tube into a fluid flow line so flow direction is from bottom to top, the float will move upward and be supported at a point where the orifice is just large enough to pass the fluid flowing through the system.
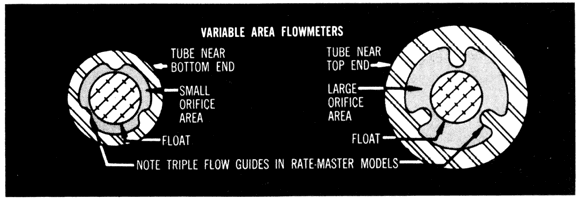
Several Forces are Involved - The precise position of the float within the tube is determined by several forces acting on it. These forces are: 1. The weight of the float; 2. The velocity pressure of the flowing fluid multiplied by the area of the float; 3. Buoyancy of the float (weight of fluid volume displaced by the float); 4. Viscous aerodynamic or hydrodynamic drag of the fluid on the float. The float's weight acts downward - while velocity pressure, buoyancy and drag all act upward on it.
Read-out and Scales - By making the tube transparent so that float position can be seen and by providing a scale along side, we may "read" the float position in terms of numbers on the scale. These scale numbers can be of two types: 1. Of an arbitrary nature (by themselves they mean nothing, but become meaningful when compared with a calibration curve) or: 2. They can be precalibrated for direct reading; to show the actual volume flow (in cfm, cc per minute, etc.) of the fluid for which the flowmeter is calibrated.
Limiting Factors - Although the basic relationship outlined above is linear; certain fluid properties tend to modify this relationship. These changes are accentuated where the variable orifice formed between float and tube becomes either very large or very small. For example...
Sonic Velocity - Where the orifice is particularly large and is combined with a heavy float, velocities of gas or other fluid through the orifice area can approach sonic velocity. In this velocity range, reflected shock waves cause the float to become unstable, and it will typically hunt from side to side and from top to bottom within the bore. At best, this condition makes it impossible to take a reading, and at worst may even destroy the flowmeter. The addition of flow guides (built into certain Dwyer Rate-Master® flowmeters) can often improve the stability and performance of the system by channeling the flow into multiple streams that equalize dynamic effects and preventing oscillation of the float. This has the new effect of moving the limit of satisfactory operation upward, and thereby expanding the range and accuracy we can achieve with any given flowmeter tube.
Laminar Flow - In flowmeters where the orifice area is extremely small, the conditions result in smooth flow, or laminar flow. Other factors which contribute to the transition to laminar flow are low velocity (often associated with a lightweight float), low density or specific gravity and high viscosity of the flowing fluid. When laminar flow conditions prevail, a greatly expanded scale is usually required. Meters operating in the laminar flow area are very difficult to manufacture and calibrate to the degree of accuracy usually expected of variable area flowmeters.
Turbulent Flow - Most variable area flowmeters operate in the turbulent flow range which occurs below sonic velocities and above the laminar flow range. In turbulent flow, the flowing fluid particles move in random paths within the stream - rather than in violent shock waves as in sonic flow or very smooth parallel paths as in laminar flow. In turbulent flow, variables follow the relationships shown in the curves. These curves are quite accurate for small changes in pressure and specific gravity. For large changes or where a change in viscosity is involved, it is much better to have the flowmeter recalibrated for the specific conditions under which it will be used.
Reynolds Numbers - Reynolds Numbers are useful in the study of fluid behavior and are quite helpful in separating laminar and turbulent flow. The Reynolds Number of a fluid flow system is described as a dimensionless index. It is equivalent to the diameter of the orifice in feet times the average velocity of the fluid in feet per second times the density of the fluid in pounds per cubic foot divided by the absolute viscosity in pounds per second foot. A system operating with a Reynolds Number of less than 2000 is said to be subject to laminar flow, whereas Reynolds Numbers above 3000 are clearly in the turbulent flow area.
How Sight Flow Indicators Work
A sight flow indicator basically consists of a small housing equipped with a glass window which is inserted in a run of pipe to observe the flow of the fluid in the pipe. To enhance the visibility of the flow, a spinner is often incorporated in the flow stream so that fluid impinging on the spinner vanes cause it to turn. The spinner also aids in the detection of low flows as well as providing visibility of flow from a distance. In addition, the speed of rotation gives a relative indication of flow velocity. Midwest Sight Flow Indicators are also available with hinged flappers instead of spinners to indicate bi-directional flow.
Sight flow indicators can be provided with a single window on the front of the indicator or double windows, one on the front and one on the back of the indicator. Double window units are best when observing the clarity or color of a liquid. Midwest single window units are always equipped with spinners to provide for observation of clear fluid flows at the lowest cost.
Vertical tube-type sight flow indicators consist of a clear glass tube, equal to or greater than the diameter of the pipe into which it is inserted, and are utilized to observe high flow rates in vertical pipe runs. No spinners or other type of detection devices are incorporated in these units. As a result, they offer no significant resistance to flow and therefore provide the lowest pressure drop of any type sight flow indicator.
Midwest Sight Flow Indicators are available with special materials to meet various applications. Optional materials are available for the sealing gaskets, spinners, and housings or flanges.