The Importance of Calibrating Measurement Instrumentation
The Importance of Calibrating Measurement Instrumentation
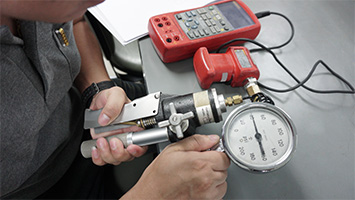
Calibrating measurement instrumentation is something that should never go overlooked. To calibrate instrumentation means to determine, check, or rectify the graduation of any instrument giving quantitative measurement. Calibrating a device ensures that the instrument will properly measure within the desired range for your application. This is important because a properly calibrated measurement device will help the user to maintain his or her system. A device can be calibrated either at the factory where the device was manufactured or within the field. Calibration certificates may be obtained once a device has been calibrated.
When a device is calibrated at the factory, the device is factory calibrated. When a device is factory calibrated, the manufacturer will ensure the device is properly reading within its designed range and meets specifications. This is best for when a user is intending to quickly put a device to work once it has been received. This type of service may add a nominal fee and increase the time it will take for the product to be shipped; but, it will also allow the user to quickly put the device to work, offsetting both the cost and time of factory calibration.
When a device is calibrated on sight at the location where it will be used, the device is field calibrated. This is ideal if the device will be communicating with multiple devices in an integrated system. By field calibrating the device, the user will be able to set the parameters required for the device to work properly within the system. Field calibration is common for devices that may not be removable once installed. Typically, manufacturers will provide guidance has to how to properly calibrate a device in the field, within the product’s specifications and without damaging the device or voiding warranty.
Some applications require a device to have a calibration certificate. A common certification for measurement devices is a NIST calibration certificate. NIST stands for the National Institute of Standards and Technology and they strive to enhance productivity, facilitate trade, and improve quality of life. For NIST calibrations, the institute will supply standard reference material (SRM) for devices to be calibrated against. A certificate of analysis and material safety data sheet are provided with every SRM sent out. The certification means that the device was tested against the SRM and met required specifications by the NIST. NIST calibration certificates do come with expiration dates, so this means that for the device to keep its certification, it will have to be retested against a NIST SRM. When a device receives a Traceable NIST Certificate, that means the device was tested against another device with a paper trail leading back to a NIST SRM. A NIST Calibration Certificate proves that a product has been tested to ensure accuracy, and helps ensure a precision device is able to achieve the highest possible levels of measurement quality and productivity. This is often required in validated or regulated applications, such as pharmaceutical or food industry.
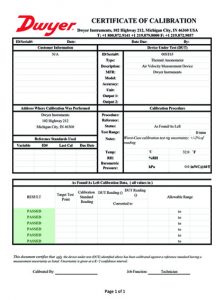
Manufacturers of instrumentation sometimes offer factory and certificates of calibration. They are able to provide this service for new purchases as well as existing products that may require recalibration from time to time. Manufacturers often keep copies of the calibration, creating a documentation back-up for the instrument. By letting the manufacturer provide calibration services, you can take advantage of their instrumentation expertise, to ensure the calibration has been done correctly, save time calibrating, and maintain back-up documents for calibration.